Types of Woodturning Tools (A Closer Look)
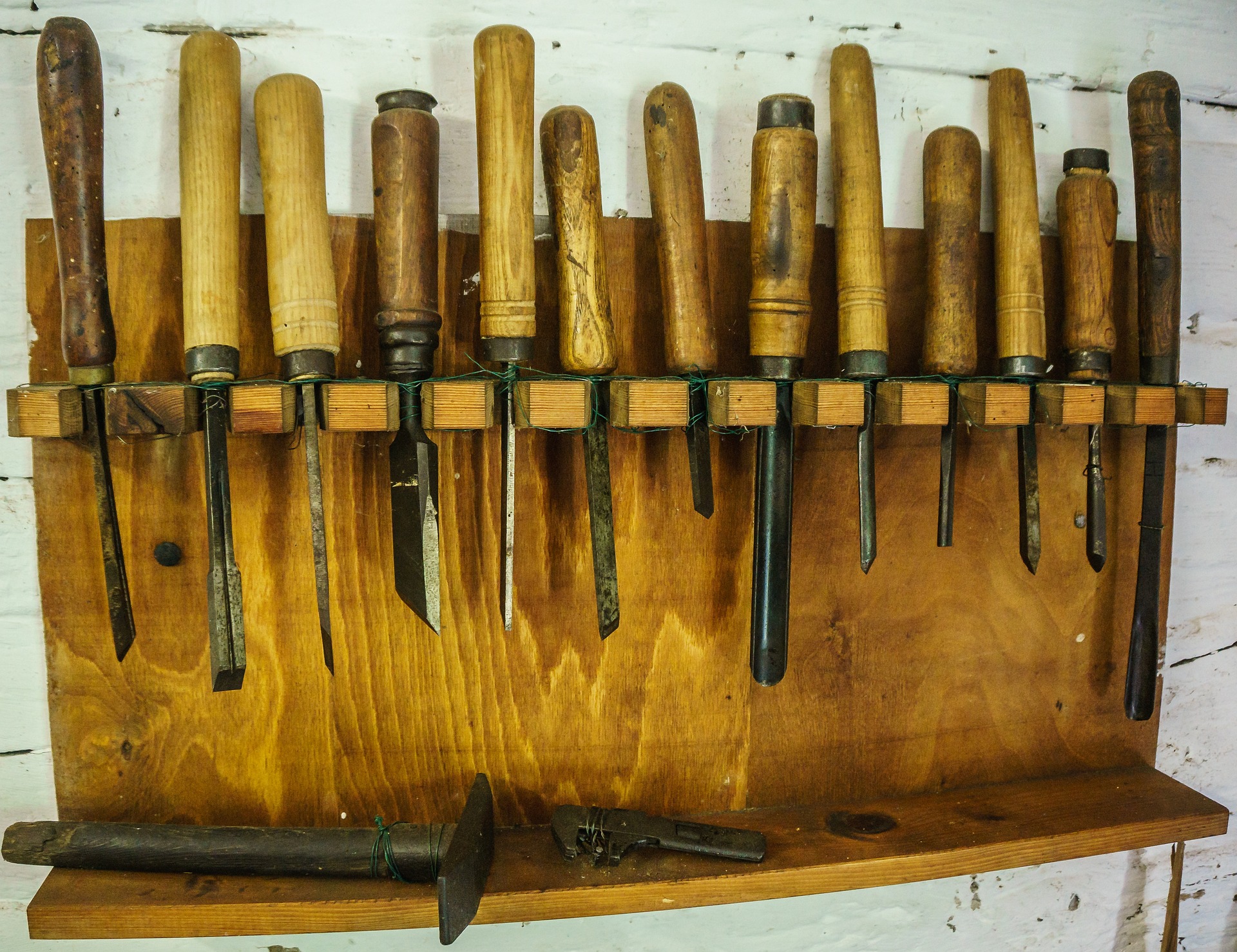
From chisels to gouges to skew chisels, we’ve got it all covered. And that’s just the beginning! Discover what to look for when buying woodturning tools, maintenance and sharpening tips, and find out about all the resources and further reading you need to become a woodturning pro. Get ready, because your woodturning world is about to be rocked.
The Different Types of Woodturning Tools
So, you’re interested in woodturning and eager to learn about different types of woodturning tools? Well, hold onto your hats because we’ve got the rundown on chisels, gouges, and skew chisels! These are the bread and butter of any woodturner’s toolkit, and understanding each one’s unique uses and benefits will take your woodturning game to the next level. Let’s dive in!
Chisels
Chisels are essential in the world of woodturning. They come in different shapes and sizes that you can choose depending on the type of project you have at hand. Some of the most common include straight chisels, bowl gouges, and spindle gouges. Straight chisels are often used for roughing-out projects, while spindle gouges are great for working on spindles such as chair legs, table legs, or other decorative pieces. On the other hand, bowl gouges come in handy when you’re working on projects such as bowls, vases, or cups.
When using chisels, it’s important to keep them sharp. A dull chisel can make your work more challenging, and increase your chances of injuring yourself. Additionally, when working on a project, it’s important to pay attention to the speed of your lathe. Make sure that it’s not too fast or too slow, as this can easily damage your chisel.
Overall, chisels are a crucial tool in the art of woodturning. Whether you’re a beginner or an expert, knowing the different types of chisels and how to use them properly can help you achieve fantastic results in your projects.
Gouges
Gouges are another must-have in your woodturning tool kit. They come in a variety of shapes, sizes and functions, and are perfect for producing rounded shapes, curves and concave surfaces in your woodturning projects. Gouges are typically made of high-speed steel or carbon steel, depending on the manufacturer, and have a U or V-shaped profile.
One popular type of gouge among woodturners is the spindle gouge. It has a long, narrow blade that works best for shaping the spindles of chairs, table legs and other cylindrical projects. Bowl gouges, on the other hand, have a wider blade with a flatter profile that makes them perfect for hollowing out bowls, vessels and other concave shapes. They are also great for roughing out stock.
Another type of gouge, the parting tool, has a thin, single-bevel blade that allows you to make precise cuts and create separation between different parts of your project. Skew gouges have a chisel-like blade with a pointed tip and a slight angle, making them perfect for making thin cuts and for finishing details on wooden surfaces.
When choosing a gouge, it’s important to look at the type of project you will be working on and choose the appropriate shape, size and angle. Like other woodturning tools, gouges require frequent sharpening to maintain a sharp edge and optimal performance. They are a versatile tool for any woodturner and are essential in creating rounded and concave shapes in your projects.
Skew Chisels
Skew chisels are a necessary part of any woodturner’s toolkit. These chisels have a flat edge and are angled at around 60 degrees, which makes them perfect for creating clean cuts on spindles, which are long thin pieces of wood. They can be used to create straight lines and right angles on delicate pieces of wood with ease.
Using a skew chisel can take some practice, but with the right approach, you can achieve a level of precision that’s hard to match with other tools. One of the most important things to keep in mind when using a skew chisel is to always keep it sharp. A dull skew chisel will cause more tear-out and splintering of the wood than a sharp one. Duplication depends on the user’s knowledge and experience.
When you’re first starting out with a skew chisel, it’s important to practice on scrap wood first. Hold the chisel at a 45-degree angle to the wood and push it along, using short, shallow strokes. As you get more comfortable with the tool, you can start to angle it more to achieve different effects.
It’s also important to pay attention to the direction of the wood grain. Cutting against the grain will cause more splintering and tear-out, while cutting with the grain will produce a smoother finish. Be patient, and take your time, with enough practice, you’ll soon be producing clean and precise cuts with your skew chisel that will make your woodturning projects stand out.
What to Look for When Buying Woodturning Tools
Buying woodturning tools can be a daunting task, especially if you’re new to the craft. With so many options on the market, it can be hard to know what features to look for. But fear not, we’ve got you covered. In this section, we’ll walk you through the most important things to consider when buying woodturning tools. From material quality to handle design and blade size, you’ll know exactly what to look for to get the best tools for your money. Let’s dive in!
Material Quality
When it comes to buying woodturning tools, material quality should be at the top of your concerns. Quality materials ensure that your tools last longer, remain sharp, and provide optimal performance. Cheaper materials tend to wear out or break quickly, which can be frustrating and costly in the long run.
One of the most common materials for woodturning tools is high-speed steel (HSS), which is known for its durability and resistance to wear. HSS tools are also easy to sharpen, making them a popular choice among woodturners. Another material option is carbon steel, which is also durable but can rust if not properly maintained.
Some woodturning tools are made of carbide, which is a highly wear-resistant material that doesn’t require sharpening as often as HSS or carbon steel tools. While carbide tools may be more expensive upfront, they can save you money in the long run by lasting longer and minimizing the need for frequent sharpening.
It’s important to consider the quality of the material for each specific tool, as some tools may require different materials than others. For example, spindle gouges and bowl gouges may perform better with different materials due to their specific uses and the stresses they encounter.
Ultimately, the material quality of your woodturning tools will greatly impact your overall experience and results as a woodturner. Invest in quality materials upfront to save money and frustration in the long run.
Handle Design
When it comes to handle design in woodturning tools, you really want to look for something that is comfortable to hold for long periods of time, but also provides a good grip. Some handles are made of wood, which can absorb shock and vibrations, but may not be as durable as other materials like metal or rubber. Rubber handles, on the other hand, offer a great grip and are very durable, but may not be as comfortable to hold for prolonged periods of time.
Some handles are also designed to be ergonomically shaped, which can provide great support for your hand and reduce strain on your fingers and wrist. This is particularly important if you plan on doing a lot of woodturning in one sitting. You also want to make sure that the handle is well balanced and doesn’t cause the tool to feel top-heavy when in use.
Remember, the handle is the point of contact between you and the wood, so it’s important to get it right. Spend some time in a woodturning store and try different handles to get a feel for what works best for you. If you’re looking for a handle online, be sure to read reviews to see what other woodturners have to say about the handle’s comfort and durability. Investing in a good handle for your woodturning tools can make a big difference in your comfort and control while working with wood.
Blade Size and Shape
When it comes to blade size and shape, there are a few key things to consider before making a purchase. The first is the size of the project you typically work on. Larger projects call for larger blades, while smaller projects require smaller blades. It’s important to keep in mind that using a blade that’s either too large or too small for the job can result in uneven cuts and an overall unsatisfactory outcome.
Another factor to consider is the shape of the blade. Different shapes are better suited for different types of cuts. For example, a bowl gouge has a U-shaped blade that’s ideal for creating concave shapes, while a spindle gouge has a V-shaped blade that’s better suited for detailed work on smaller projects.
In addition to size and shape, the quality of the blade is also important. Look for blades made of high-speed steel or a durable metal alloy, which will hold their edge longer and require less frequent sharpening.
Ultimately, choosing the right blade size and shape comes down to personal preference and the type of projects you typically work on. Experiment with different blades to find the ones that work best for you and your style of woodturning.
How to Use Woodturning Tools
Ready to take your woodturning skills to the next level? Before we dive in, we can’t stress enough how important safety precautions are when it comes to using your tools.
Safety Precautions
When it comes to woodturning, safety should always be your top priority. This is particularly true when using woodturning tools, which can be dangerous if not handled correctly. There are a number of safety precautions that you should take before starting any woodturning project.
First and foremost, it’s important to wear the right protective gear. This includes safety glasses to protect your eyes from wood dust and wood chips, as well as a dust mask to prevent inhalation of wood particles. Additionally, it’s a good idea to wear gloves to protect your hands from splinters and flying wood chips.
Before turning on your lathe, make sure that all bolts and fittings are properly secured, and that there are no loose parts. Always tie long hair back, remove any dangling jewelry, and roll up your sleeves to avoid getting caught in the lathe.
Finally, it’s important to be aware of your surroundings when working with woodturning tools. Always make sure that there’s enough space around the lathe to move freely, and that there are no trip hazards or obstacles in your way.
Techniques for Smooth Cuts
When it comes to getting smooth, clean cuts in your woodturning projects, there are a few key techniques to keep in mind. First, it’s important to maintain a consistent speed while turning your piece. With practice, you’ll develop a feel for the right speed for each type of cut and piece of wood you’re working with.
Another important factor in achieving smooth cuts is keeping your tools sharp. Dull blades will only cause frustration and uneven cuts. Regularly sharpen your chisels, gouges, and skew chisels, and consider investing in a good sharpening system for consistent results.
Additionally, pay close attention to your hand placement and body position while working. Your non-dominant hand should be gently guiding the turning piece, while your dominant hand works the tool. Be aware of your body position and keep your feet planted firmly on the ground to maintain stability.
Finally, don’t be afraid to experiment with different cutting angles and techniques to find what works best for you and your project. Woodturning is a skill that takes time and patience to develop, but with practice and a few techniques in your toolbox, you’ll be well on your way to achieving smooth, professional-looking cuts every time.
Maintenance and Sharpening Tips for Woodturning Tools
Maintenance and Sharpening Tips for Woodturning Tools: Keep Your Tools in Top Condition!
Now that you know all about the different types of woodturning tools and how to use them, it’s time to talk about how to maintain them. In this section, we’ll cover everything from cleaning and lubrication to sharpening methods and tools you need for the job. We’ll also discuss how to properly store your woodturning tools to ensure they’re always ready to go when you are. Let’s get started!
Cleaning and Lubrication
When it comes to extending the life of your woodturning tools, cleaning and lubrication are two crucial aspects that you simply cannot ignore. Regular cleaning helps ensure that your tools are free from rust, debris, and other types of build-up that can gradually diminish their performance. To clean your tools, start by wiping them down with a clean cloth to remove any sawdust or debris. Next, use a soft-bristled brush to gently scrub each tool while paying close attention to the areas surrounding the blade. Avoid using abrasive cleaners or rough brushes, as they can scratch or damage the metal surfaces.
Once you’ve cleaned your tools thoroughly, it’s time to lubricate them to reduce wear and tear on the blades and keep them working smoothly. Use a fine oil or silicone spray to apply the lubricant, making sure to cover the entire surface of the tool. Be careful not to over-lubricate, as this can attract dust and create a sticky residue that can interfere with the tool’s performance.
Remember, the key to maintaining your woodturning tools is to follow a regular cleaning and lubrication schedule. By taking the time to care for your tools properly, you’ll be able to enjoy smooth, precise cuts for years to come.
Sharpening Methods and Tools
Sharpening is an art form in its own right. It takes a steady hand, some patience, and a little bit of luck to get your woodturning tools nice and sharp. There are many different methods and tools available to sharpen your tools, so it’s important to find the one that works best for you.
One common method for sharpening tools is to use a honing guide. This tool holds your tool at the correct angle while you sharpen it against a sharpening stone. This method is great for beginners because it ensures that you’re getting the correct angle and it’s difficult to mess up.
Another popular sharpening method is using a jig. A jig is a tool that guides your tool along a sharpening stone, again ensuring that you’re getting the correct angle. Jigs are a bit more advanced than honing guides but are still relatively easy to use.
If you’re feeling a little more adventurous, you can try freehand sharpening. This method involves sharpening your tool by hand against a stone. It takes a bit of practice to get the correct angle and motion, but many woodturners swear by this method.
When it comes to sharpening stones, there are many different types available. Some are oil stones, some are water stones, and some are diamond stones. Each one has its own advantages and disadvantages, so it’s important to do some research and figure out which one works best for you.
No matter which sharpening method or tools you choose, it’s important to keep them in good condition. Clean them after every use, and make sure they’re stored in a dry place. A little bit of maintenance goes a long way, and it’ll keep your tools sharp and ready to use for years to come.
Storing Your Woodturning Tools
After spending time and money investing in high-quality woodturning tools, it’s important to store them properly to extend their lifespan. A disorganized workspace not only puts your tools at risk of damage, but it can also lead to frustration and wasted time searching for the right tool.
One of the best ways to store your woodturning tools is on a magnetic tool rack. Not only does this keep your tools organized and easy to find, but it also allows air to circulate around the tools, preventing rust and corrosion.
Another option is to use a tool chest or box with individual compartments for each tool. This method is particularly effective for larger tool collections or for protecting your tools during transport to workshops or demonstrations.
Whichever storage method you choose, be sure to keep your tools clean and dry before storing them. It’s also a good idea to periodically apply a protective coating, such as a light coat of mineral oil, to prevent rust and keep your tools in pristine condition.
Remember, investing in high-quality woodturning tools is only half the battle. Proper maintenance and storage will go a long way in ensuring you get the most out of your investment.
Resources and Further Reading
Now that you have a good grasp of the different types of woodturning tools, it’s time to expand your knowledge and learn from the experts. Here are some top resources and further reading to help you refine your technique and take your woodturning skills to the next level. From the best tool brands to online communities and forums where you can connect with fellow woodturners, and even books and Youtube channels with endless tips and tutorials, we’ve got you covered. Get ready to dive deeper into the world of woodturning and unlock your full potential as a craftsman.
Recommended Woodturning Tool Brands
If you’re looking for quality woodturning tools, then you’ve come to the right section! In this section, we’ll be sharing our top picks for the best woodturning tool brands. These brands have been recommended by experienced woodturners and are known for their durable and high-quality products.
First on our list is Robert Sorby. This UK-based brand has been around for over 200 years and is a trusted name in the woodworking industry. They offer a wide range of tools for all levels of expertise, from beginners to professionals. Their products are made with high-quality materials and are built to last.
Next, we have the American brand, Crown Tools. They are known for their high-quality turning tools that are perfect for both beginners and experienced woodturners. Their tools are made from M2 high-speed steel, which ensures durability and a long life span.
Another great brand to consider is Hamlet Craft Tools. They offer a variety of turning tools that are perfect for both spindle and bowl turning. Their tools are made with high-quality materials and are built to provide an optimal turning experience.
Last but not least, we recommend the Australian brand, Henry Taylor Tools. They offer a wide range of high-quality turning tools that are perfect for both beginners and experienced woodturners. Their tools are made with high-quality materials and are built to last.
These are just a few of the top brands that we recommend when it comes to woodturning tools. Of course, there are many others out there, but these are the ones that we think are the best of the best. When you invest in quality tools, you’re investing in your craft, so be sure to choose wisely!
Online Communities and Forums
The woodturning community is full of passionate and talented individuals who are always ready to share their expertise and insights. Luckily, there are countless online forums and communities where you can connect with woodturners from all over the world.
One of the most popular woodturning forums is the Woodturner’s Resource. This online community is a great place to learn from experienced woodturners and share your own tips and tricks. With over 35,000 members, you are sure to find someone who can help you with any woodturning question you have.
If you are looking for a more casual atmosphere, the Woodturning subreddit is a great place to start. This community is a mix of amateur and professional woodturners who share their projects, advice, and experiences. The subreddit also hosts regular challenges and competitions to keep things interesting.
For those who are looking to connect with woodturners in their local area, the American Association of Woodturners has a directory of local chapters on their website. This is a great way to meet other woodturners, attend local events, and learn new techniques.
No matter what your skill level or interest in woodturning, there is an online community out there for you. So why not join the conversation and connect with like-minded individuals who share your passion for this timeless craft.
Books and Youtube Channels to Learn from
If you’re looking to expand your woodturning skills beyond the basics, there’s no better way to learn than through books and Youtube channels. For written resources, we recommend “The Fundamentals of Woodturning” by Mike Darlow and “Woodturning – The Craftsman’s Guide” by Mark Baker. These books offer in-depth guidance on everything from tool selection to advanced techniques, making them essential additions to any woodturner’s library.
As for Youtube channels, there are several excellent options to choose from. We particularly recommend “Woodturning with Tim Yoder,” which features a mix of instructional videos and projects, as well as “Makers Central,” which showcases an array of woodturning and other maker-related content. In addition to these channels, there are dozens of other woodturning-focused channels to explore, each offering their unique insights and techniques.
Whether you prefer to learn through reading or video, there’s never been a better time to expand your woodturning knowledge. So crack open a book or fire up your favorite Youtube channel and start honing your skills today!